
Open the controller, you can see the program module under RAPID/T_ROB1, and then you can write the program. connection is initiated by a client socket and the server waits for the. After the addition is complete, restart the controller. The study uses the ABB Robot studio simulation software and an existing. Make the robot return to the mechanical origin, then create an empty path, and drag the three target points to the path in turn.ĭelete the copy object of the previously simulated block.Īdd two signals, one is the in-position signal, which is used to wait for the conveyor belt, and the other is the fixture signal. Rotate the third target point so that it rotates -90 degrees around the Z axis.Ĭonfigure parameters for the target point (The latter two target points are for stacking, the blocks will have two visiting attitudes, so two target points are used) Run the simulation to make the object reach the surface sensor, then stop the simulation and capture a few target points. In the simulation setting, remove the box selection behind the robot system. USER MANUAL 2/14 Requirements RobotWare 6.09 or higher (less than RobotWare 7.0). Select the following options in the options Create a Smart component for the movement of conveyor belt objects.Create palletizing objects and move them to the starting point of the conveyor belt.Import the conveyor belt and set the position of the conveyor belt.In the layout menu, drag the fixture to the IRB2600 robot to complete the fixture installation.Align the local coordinates of the Smart component of the gripper with the coordinates of the end flange of the robot, so that the local coordinates of the fixture coincide with the local coordinates of the flange, and prepare for the next installation of the fixture.
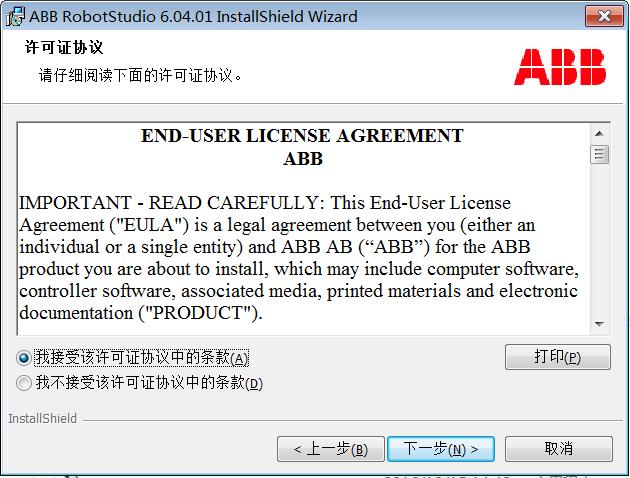
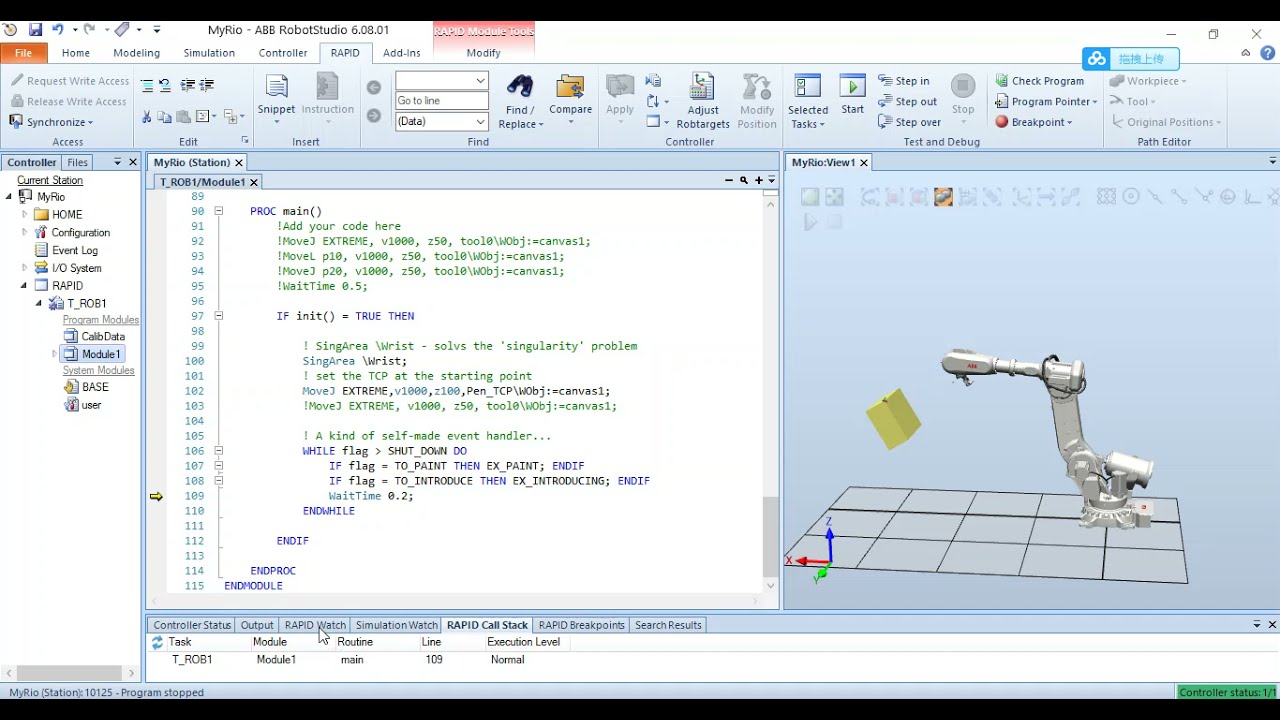
Move the local coordinate origin of the fixture so that the origin is the center of the top surface (the part connected with the flange).
